All you need to know about Stained Glass
Stained Glass For Dummies
Creating stained-glass and warm-glass designs can be a fun and addictive hobby, but to get started you need to go shopping for some basic tools and supplies and develop basic skills. Then you can practice and perfect the different techniques to your heart’s content.
Creating stained-glass and warm-glass designs can be a fun and addictive hobby, but to get started you need to go shopping for some basic tools and supplies and develop basic skills. Then you can practice and perfect the different techniques to your heart’s content.
A Stained-Glass Shopping List
Stained glass is a hobby that requires quite a bit of equipment. Thankfully, most of the equipment is rather versatile and can be used for both copper foil and lead came projects. Some supplies, though, are specially designed for a particular technique. Print off the following shopping lists and take them to your nearest glass or hobby shop to make sure you have what you need for whatever project you’ve set out to create.
Stained glass is a hobby that requires quite a bit of equipment. Thankfully, most of the equipment is rather versatile and can be used for both copper foil and lead came projects. Some supplies, though, are specially designed for a particular technique. Print off the following shopping lists and take them to your nearest glass or hobby shop to make sure you have what you need for whatever project you’ve set out to create.
General stained-glass tools and supplies
The following tools are needed for both copper-foil and lead-came projects:
-
Basic drafting supplies: These supplies include a metal ruler, white pattern paper, a pencil, and permanent markers.
-
Combination breaking-grozing pliers: You need both breaking and grozing pliers, but you can save a little money by buying just one pair of combination pliers. You can use your combo pliers to help you break glass and fine-tune unwanted glass shards.
-
Flux and brush: Flux is a chemical you have to use to clean any surface on your project that you want to solder; you can’t solder where you don’t flux. You can use a basic disposable brush to paint the flux onto the foil and lead surfaces of your project.
-
Glass: When you first start out with stained glass, you should work mainly with clear glass because it’s less expensive than colored glass. Then, when you’re ready to create your first full-color project, visit a glass shop or go online and purchase some smooth, colored glass (smooth glass is easier to work with than textured glass).
Always buy 25 to 50 percent more glass than you think you’ll need for your project.
-
Glass grinder: This must-have power tool has a diamond wheel that allows you to grind away any unwanted glass edges so your pieces fit together perfectly on your pattern.
-
100-watt soldering iron: A 100-watt soldering iron gives you plenty of heat for all your stained-glass soldering needs. Note that stained-glass artists don’t use soldering guns.
-
Project patterns: All stained-glass projects — even simple sun catchers — start as designs drawn on pattern paper, so the first step in any project is to find a pattern. You can find hundreds of patterns to work with online or in stained-glass books.
-
Safety glasses: Select glasses that are comfortable to wear so you’ll be sure to wear them whenever you work in your glass studio.
-
Self-oiling glass cutter: You can select a pistol-grip cutter that’s easy to hold in the palm of your hand or a barrel cutter that you hold more like a pencil between your fingers. Both cutters have the same cutting heads.
The following tools are needed for both copper-foil and lead-came projects:
- Basic drafting supplies: These supplies include a metal ruler, white pattern paper, a pencil, and permanent markers.
- Combination breaking-grozing pliers: You need both breaking and grozing pliers, but you can save a little money by buying just one pair of combination pliers. You can use your combo pliers to help you break glass and fine-tune unwanted glass shards.
- Flux and brush: Flux is a chemical you have to use to clean any surface on your project that you want to solder; you can’t solder where you don’t flux. You can use a basic disposable brush to paint the flux onto the foil and lead surfaces of your project.
- Glass: When you first start out with stained glass, you should work mainly with clear glass because it’s less expensive than colored glass. Then, when you’re ready to create your first full-color project, visit a glass shop or go online and purchase some smooth, colored glass (smooth glass is easier to work with than textured glass).Always buy 25 to 50 percent more glass than you think you’ll need for your project.
- Glass grinder: This must-have power tool has a diamond wheel that allows you to grind away any unwanted glass edges so your pieces fit together perfectly on your pattern.
- 100-watt soldering iron: A 100-watt soldering iron gives you plenty of heat for all your stained-glass soldering needs. Note that stained-glass artists don’t use soldering guns.
- Project patterns: All stained-glass projects — even simple sun catchers — start as designs drawn on pattern paper, so the first step in any project is to find a pattern. You can find hundreds of patterns to work with online or in stained-glass books.
- Safety glasses: Select glasses that are comfortable to wear so you’ll be sure to wear them whenever you work in your glass studio.
- Self-oiling glass cutter: You can select a pistol-grip cutter that’s easy to hold in the palm of your hand or a barrel cutter that you hold more like a pencil between your fingers. Both cutters have the same cutting heads.
Special copper-foil tools
Before you start your first stained-glass project using the copper-foil construction technique, make sure you gather up the following basic tools and supplies:
-
7/32-inch copper foil: To wrap each piece of glass in your project, you use thin strips of copper foil with adhesive backing. (3/16-inch foil is also common among stained-glass artists, but it’s a little more difficult to work with than the larger 7/32-inch foil.)
-
Foilmate roller: This little tool helps you burnish, crimp, and roll copper-foil tape tightly to each piece of glass in your project.
-
60/40 solder: You need to use solder that’s 60 percent tin and 40 percent lead to hold your foiled glass pieces together.
Before you start your first stained-glass project using the copper-foil construction technique, make sure you gather up the following basic tools and supplies:
- 7/32-inch copper foil: To wrap each piece of glass in your project, you use thin strips of copper foil with adhesive backing. (3/16-inch foil is also common among stained-glass artists, but it’s a little more difficult to work with than the larger 7/32-inch foil.)
- Foilmate roller: This little tool helps you burnish, crimp, and roll copper-foil tape tightly to each piece of glass in your project.
- 60/40 solder: You need to use solder that’s 60 percent tin and 40 percent lead to hold your foiled glass pieces together.
Special lead-came tools
Before you can start creating stained-glass projects using the lead-came technique, you need to purchase the following tools and supplies in addition to the general stained-glass supplies:
-
50/50 solder: When soldering lead-came projects, you need to work with solder that contains an equal blend of tin and lead.
-
Horseshoe nails: You use these nails to secure glass and lead-came pieces during the construction process.
-
Lead came: Cames are strips of lead that come in either H or U profile shapes. The glass pieces of your project fit into the cames. The most common lead-came sizes are 3/8-inch H, 3/16-inch H,7/32-inch H, and 1/4-inch U.
-
Lead nippers or lead knife: You use these tools to trim your lead came to the correct size when building your projects.
-
Rheostat: A rheostat is a temperature controller that helps you reduce and control the temperature of your soldering iron so that you don’t heat your lead came too much. Note: If you’re working with an iron that has a built-in controller, you don’t need this tool.
Before you can start creating stained-glass projects using the lead-came technique, you need to purchase the following tools and supplies in addition to the general stained-glass supplies:
- 50/50 solder: When soldering lead-came projects, you need to work with solder that contains an equal blend of tin and lead.
- Horseshoe nails: You use these nails to secure glass and lead-came pieces during the construction process.
- Lead came: Cames are strips of lead that come in either H or U profile shapes. The glass pieces of your project fit into the cames. The most common lead-came sizes are 3/8-inch H, 3/16-inch H,7/32-inch H, and 1/4-inch U.
- Lead nippers or lead knife: You use these tools to trim your lead came to the correct size when building your projects.
- Rheostat: A rheostat is a temperature controller that helps you reduce and control the temperature of your soldering iron so that you don’t heat your lead came too much. Note: If you’re working with an iron that has a built-in controller, you don’t need this tool.
Adding Warm-Glass Tools and Supplies to Your Stained-Glass Studio
Glass fusing (also called warm glass) is one of today’s most popular art-glass techniques. It involves heating glass to specific temperatures so that you can form and shape it into fun projects like bowls, vases, and jewelry. Before you can add this neat technique to your studio’s to-do list, though, you need to gather a few warm-glass-specific tools and supplies:
-
Didymium safety glasses: These special safety glasses protect your eyes from the glare of red hot glass.
-
Glass: To make a warm-glass project, you need to buy compatible fusible glass. The two basic categories of fusing-glass compatibility are COE 96 and COE 90.
For any given warm-glass project, you must use one and only one type of fusible glass (either COE 96 or COE 96); you can’t mix the two together.
-
Glass kiln: Kilns are the most expensive tools you have to purchase for your warm-glass studio, so you may want to start small with a kiln that has 5-inch shelves. Then as your interest and skills grow, you can invest in a larger kiln so you can make larger projects. Make sure your kiln comes with its own shelves, posts, and temperature gauges.
-
Heat-resistant gloves: You need to wear special heat-resistant gloves to protect your hands whenever you’re working around the kiln.
-
Kiln wash and brush: You have to apply kiln wash to your kiln shelves and glass molds before you fire your project to keep the hot glass from sticking to them.
Glass fusing (also called warm glass) is one of today’s most popular art-glass techniques. It involves heating glass to specific temperatures so that you can form and shape it into fun projects like bowls, vases, and jewelry. Before you can add this neat technique to your studio’s to-do list, though, you need to gather a few warm-glass-specific tools and supplies:
- Didymium safety glasses: These special safety glasses protect your eyes from the glare of red hot glass.
- Glass: To make a warm-glass project, you need to buy compatible fusible glass. The two basic categories of fusing-glass compatibility are COE 96 and COE 90.For any given warm-glass project, you must use one and only one type of fusible glass (either COE 96 or COE 96); you can’t mix the two together.
- Glass kiln: Kilns are the most expensive tools you have to purchase for your warm-glass studio, so you may want to start small with a kiln that has 5-inch shelves. Then as your interest and skills grow, you can invest in a larger kiln so you can make larger projects. Make sure your kiln comes with its own shelves, posts, and temperature gauges.
- Heat-resistant gloves: You need to wear special heat-resistant gloves to protect your hands whenever you’re working around the kiln.
- Kiln wash and brush: You have to apply kiln wash to your kiln shelves and glass molds before you fire your project to keep the hot glass from sticking to them.
Tips for Improving Your Glass-Cutting Skills
One of the first skills you need to master as you begin your stained-glass hobby is cutting out your glass shapes accurately. Here are some tips that can help you get off to a successful start:
-
Select a high-quality, self-oiling glass cutter that fits comfortably in your hand. Always check the oil level in your cutter before you start cutting, and make sure the oil lubricates the cutting wheel as it turns. Add more oil when needed.
-
Purchase a pair of safety glasses that fit your face comfortably. Wear your glasses every time you work with glass to keep your eyes safe from flying glass chips and dust.
-
Make sure you have good lighting in your studio so you can see what you’re cutting. Cutting in low light is dangerous and can lead you to make poor, inaccurate cuts.
-
Stand whenever you cut glass. Applying the right amount of pressure to the cutter is difficult to do when you’re seated.
-
Position all your pattern templates at least 1 to 2 inches away from the edges of the glass.Doing so gives you enough glass to hold when breaking and helps support the glass.
-
Score from one edge of the glass to the other, and don’t apply so much pressure that the cutting wheel crushes the glass. Try not to have any gaps or skips in your score line. You may be overscoring if your score line is bright white and chips of glass are flying from that line.
-
Don’t go back and forth over a score line with your cutter. If your initial score line doesn’t turn out right, move over 1/4 inch and try again.
-
Use your hands to break the glass whenever possible. If you need more leverage, use your glass-breaking pliers. If you’re using a pair of breaking-grozing combo pliers, make sure the flat side of the pliers is on top of the glass and the curved side is under the glass.
-
Clean up any rough edges using the ridges inside your grozing pliers or glass grinder. Each cut piece has to be the exact size as your pattern template so all the pieces fit together during the building process.
-
Keep your cutting surface clean and free of glass chips and shards. Use a bench brush or a clean paint brush to sweep your cutting area in between cuts. If you try to cut your glass pieces on top of small chips of glass, your glass may break unexpectedly.
One of the first skills you need to master as you begin your stained-glass hobby is cutting out your glass shapes accurately. Here are some tips that can help you get off to a successful start:
- Select a high-quality, self-oiling glass cutter that fits comfortably in your hand. Always check the oil level in your cutter before you start cutting, and make sure the oil lubricates the cutting wheel as it turns. Add more oil when needed.
- Purchase a pair of safety glasses that fit your face comfortably. Wear your glasses every time you work with glass to keep your eyes safe from flying glass chips and dust.
- Make sure you have good lighting in your studio so you can see what you’re cutting. Cutting in low light is dangerous and can lead you to make poor, inaccurate cuts.
- Stand whenever you cut glass. Applying the right amount of pressure to the cutter is difficult to do when you’re seated.
- Position all your pattern templates at least 1 to 2 inches away from the edges of the glass.Doing so gives you enough glass to hold when breaking and helps support the glass.
- Score from one edge of the glass to the other, and don’t apply so much pressure that the cutting wheel crushes the glass. Try not to have any gaps or skips in your score line. You may be overscoring if your score line is bright white and chips of glass are flying from that line.
- Don’t go back and forth over a score line with your cutter. If your initial score line doesn’t turn out right, move over 1/4 inch and try again.
- Use your hands to break the glass whenever possible. If you need more leverage, use your glass-breaking pliers. If you’re using a pair of breaking-grozing combo pliers, make sure the flat side of the pliers is on top of the glass and the curved side is under the glass.
- Clean up any rough edges using the ridges inside your grozing pliers or glass grinder. Each cut piece has to be the exact size as your pattern template so all the pieces fit together during the building process.
- Keep your cutting surface clean and free of glass chips and shards. Use a bench brush or a clean paint brush to sweep your cutting area in between cuts. If you try to cut your glass pieces on top of small chips of glass, your glass may break unexpectedly.
Foil versus Lead: Which Stained-Glass Technique Do You Choose?
When constructing a stained-glass project, you use either copper foil or lead to hold the glass pieces together. How do you know which one to choose? Keep the following factors in mind as you determine which construction technique to use for a particular stained-glass design:
-
Geometric designs lend themselves to lead-came techniques. Making a lot of straight lines meet up nicely (often a key in geometric designs) is difficult when you’re using copper foil. On the other hand, using lead came allows you to hide the small imperfections between glass pieces and keep everything on pattern.
-
Designs with a lot of small pieces work best with copper foil. Copper foil is easier to wrap around small pieces, and it keeps the project from looking bulky.
-
Sun catchers are naturals for copper foil. Because lead stretches, it needs the support of a rigid frame. Sun catchers don’t work well in rigid frames, and if you construct a sun catcher out of lead, it’ll stretch over time and pull apart.
When constructing a stained-glass project, you use either copper foil or lead to hold the glass pieces together. How do you know which one to choose? Keep the following factors in mind as you determine which construction technique to use for a particular stained-glass design:
- Geometric designs lend themselves to lead-came techniques. Making a lot of straight lines meet up nicely (often a key in geometric designs) is difficult when you’re using copper foil. On the other hand, using lead came allows you to hide the small imperfections between glass pieces and keep everything on pattern.
- Designs with a lot of small pieces work best with copper foil. Copper foil is easier to wrap around small pieces, and it keeps the project from looking bulky.
- Sun catchers are naturals for copper foil. Because lead stretches, it needs the support of a rigid frame. Sun catchers don’t work well in rigid frames, and if you construct a sun catcher out of lead, it’ll stretch over time and pull apart.
You will need these stained glass tools and supplies to get started
You will need to obtain some stained glass tools and supplies before you start working with glass. Some of the tools and supplies I'm going to show you can be improvised from things you have around the house. Also, you don't need to buy everything at once. You can start out with the basics (I have noted which ones are basic with a red Basic after the name of the item) and buy the more specialized tools as you need or want them.
*Please note that I do not sell stained glass tools and supplies. This page is just to show you what you will need. You can get these tools and supplies from most stained glass suppliers in your own city or found on the internet.

Comfort Grip Oil Cutter

Pistol Grip Oil Cutter
Oil Cutters. Basic You will find a variety of styles as well as brands of oil glass cutters. Toyo is my favorite brand, but you can also choose from Studio Pro, Inland or Fletcher.
To keep things simple, I'd recommend starting out with a comfort grip or pencil grip cutter. They are one in the same, just different names for different brands. They are called that because you hold them like a pencil and they are comfortable to hold. These stained glass tools will cost around $30.
Don't get a cheap glass cutter from the hardware store. They aren't meant for stained glass and will cause you a lot of frustration.

Instead of cutting oil, you can use 3 in 1 oil, sewing machine oil, kerosene, or lamp oil. I use lamps oil because I have an abundance of it for my oil lamps. I like it because it's cheap and it doesn't have the odor that you get from kerosene.









Copper Foil BasicGet 1/4" copper foil until you get confident with foiling. You have several brands to choose from. Make sure you get copper foil, not black back or silver back...just plain copper foil. You will probably want the other backings as you proceed making projects, but for now, just plain copper foil is all you need. My favorite brand is Edco. You will spend around $7.00 for a roll.















Most of these supplies and tools for stained glass can be purchased at Delphi Glass I order from them and I'm extremely happy with their service and prices. However, if you have a local stained glass supply business, that's the place you should visit first, especially for buying glass. Each piece of glass will look a little different, so it helps to see what is available and pick out exactly what you need.
This is where you can Contact Me
Free Stained Glass Patterns Search
Please be aware that the patterns you find at this free stained glass patterns search are protected by copyright laws. They are not for resale, or commercial or non commercial distribution, which includes books, web sites, on-line forums, ebooks, pamphlets, or photocopied distribution. Please read each web site's individual rules for the use of their patterns.
To make searching easier, use this free stained glass patterns search to find patterns quickly. All of the free patterns for stained glass, that could be found on the internet, have been put into categories.
All you have to do is:
1. Find the category
2. Find the name of the pattern you're looking for, and
3. Click.
New Categories and Patterns will be added as they become available.
1. Find the category
2. Find the name of the pattern you're looking for, and
3. Click.
New Categories and Patterns will be added as they become available.
The patterns in this free stained glass patterns search come in various formats. Some might need to be resized before you can use them. There are several resizing programs available. My favorite is Rapid Resizer.
Quite a few of these patterns are in black and white. Many of the web sites also show the finished item in color. You should be able to see the color version by going to that web site's free patterns page or home page.
3-D Patterns
Candle Shelters, Clocks, Planters and Terrariums, and a Corner Shelf
Candle Shelters, Clocks, Planters and Terrariums, and a Corner Shelf
Including Native American Patterns
Animal Patterns
Pets, Farm Animals and Wild Animals
Pets, Farm Animals and Wild Animals
Glass Box Would you like to learn how to make a stained glass box with a hinged lid? This easy to follow, step-by-step ebook comes with a 100% money back guarantee. Read more about it Here ![]() |
Bugs
Butterfly Patterns
Candle Shelters and Candle Holders
Car Patterns
Cartoon Character Patterns
Including Science Fiction Patterns
Celestial Patterns
Patterns for Angels, Rainbows, Sun, Moon and Stars
Celtic Patterns
Children and Nursery Patterns
Christmas Patterns
Clocks
Clown Patterns scroll to bottom of page
Contemporary Patterns
Clothing Patterns
Clothes, Handbags/Purses, Jewelry, Shoes
Fairy Patterns
Fantasy Patterns
Elves and Gnomes
Unicorns
Wizards
Far East/Oriental Patterns
Chinese and Japanese Inspired Patterns
Chinese Calligraphy Characters
Chinese Calligraphy Table Lanterns
Japanese Kanji
Fanlights
Fish Patterns
Flower Patterns
Food and Beverage Patterns
Frank Lloyd Wright Style
Frame Patterns for Pictures and Mirrors
Frog and Reptile Patterns
Frogs and Toads, Snakes, Snails and Lizards
Games
Geometric Patterns
Glass Fusing Patterns
Handbags and Purses
Hexagonal Window Patterns
Hobby Patterns
Holiday Patterns
Chanuka, Christmas Easter, Fourth of July, Halloween
St Patrick's Day, Thanksgiving, Valentines Day
Insect Patterns
Lampshade Patterns
Panel Lamps, Lanterns/Table Lanterns
Chinese Calligraphy Table Lanterns
Mini and Midi Shades
Logo Patterns
Mermaids
Mirror Patterns
Miscellanoeus Patterns
Dinosaurs, Windows and Large Suncatchers
Kaleidoscope Wheels
Quilt Pattern Windows, Misc. Suncatchers
Mythology Patterns
Window Corners, Wreaths, Sundial
Windchimes
Moon
Motorcycles
Mosaic and Stepping Stone Patterns
Musical Instruments
Musicians
Mythology Patterns
Native American Patterns
Nautical Patterns
Boats, Light Houses, Miscellaneous
Night Lights
Nursery Patterns
Oriental Patterns
People Patterns
Famous people, Miscellaneous people
Phoenix and Pegasus
Planters
Prairie Style Patterns
Rainbow Patterns
Religious Patterns
Reptiles
Round Window Patterns
Scenic Patterns
Miscellaneous Scenes, Geographical Places
Tropical Scenes
Water Scenes
Science Fiction Patterns
Sconces
Shoes
Snakes
Sports Patterns
Stars
Stepping Stones
Sun
Suncatchers (Large)
Suncatchers (Small)
Symbols
Torchwork Instructions For Bead Making
Traditional Patterns
Transoms
Transportation Patterns
Trains
Tree Patterns
Turtles
Unicorn
Victorian Patterns
Wind Chimes
Windows
Window Corners
Wreaths
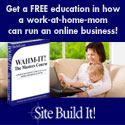
If you have any questions about these patterns, or know of any that I haven't listed, you can contact me here.
To find everything else on this web site go to the Web Site Index
Can't find what you wanted on this page? To continue your search, use the Google search box below.

Custom Search
Return from Free Stained Glass Pattern Search to Free Patterns For Stained Glass Home Page
Comments