Awesome Production of SU-30

Stepanov Slava has travelled to the factory that assembles SU-130 warplanes and has taken some very, very artistic photos of the process, plus he has a story with the photos, and we are telling it all here now inside this post. I really advise you to read it all the way through as the pics are awesome and lots of small details of the production lines of these planes are revealed. It must have been top secret just a while ago but for some reason it is pretty public now. So let's see it:

First, a few words on the plane. The SU-30 is a two seater jet that is assembled in Irkutsk city. The factory is called IAZ - Irkutsk Aircraft Zavod (Factory) and it has produced over 7,000 warplanes since its start. It exports planes to 37 countries around the world. Also it makes YAK-130 planes and some pieces of Airbus jets.
The SU-30CM is made on a SU-27 base. It was the first plane to achieve "supermaneuverability" (click if you want to read about this term on Wiki).

Basically, this is a jet fighter. It can also cover operations on the ground and/or destroy targets on the ground. It's a multifunctional plane. 

This is a modern plane and it's adapted to the current requirements of the Russian air force: it can climb up to 16,300 meters high and fly up to 3,000km in distance. Its top speed is 2125 km/h (wow!).
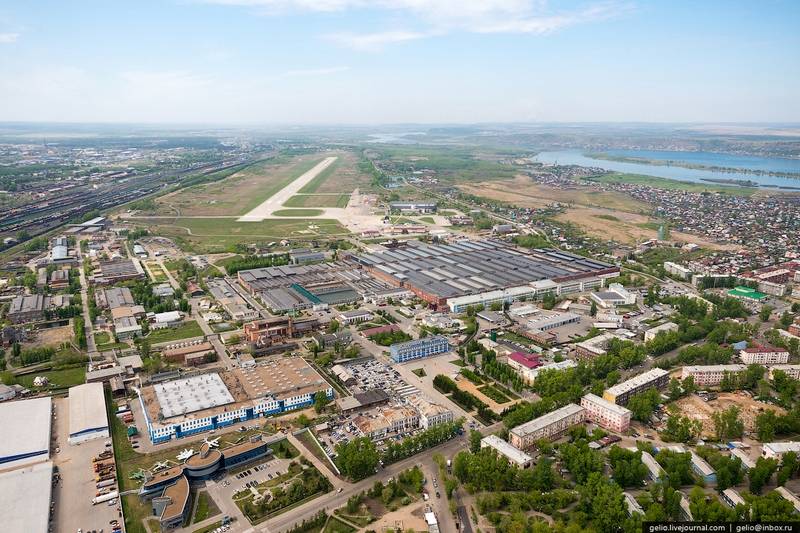
It marks its 80th anniversary this year.
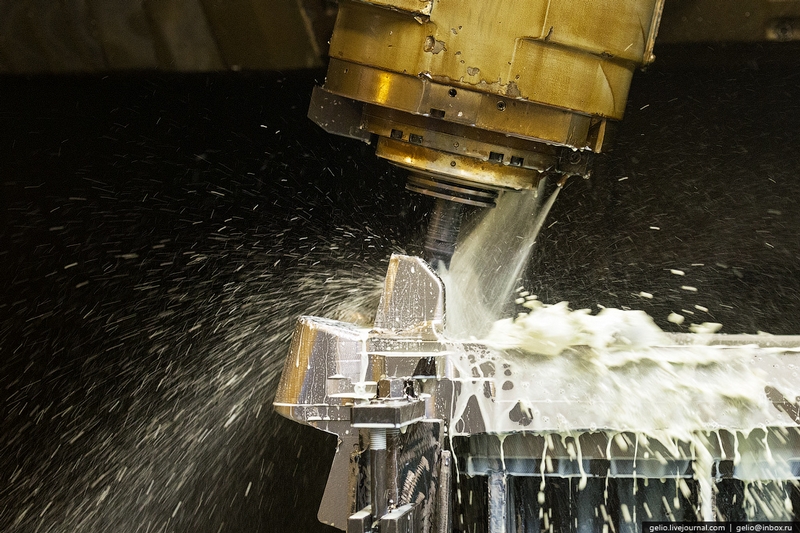
Looking at these photos, I can understand that making a plane is no less technologically complex than making an iPhone. For sure.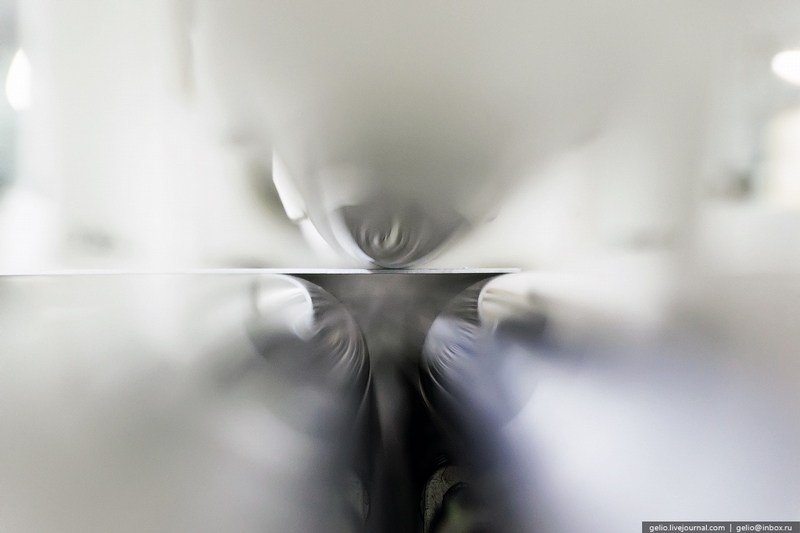
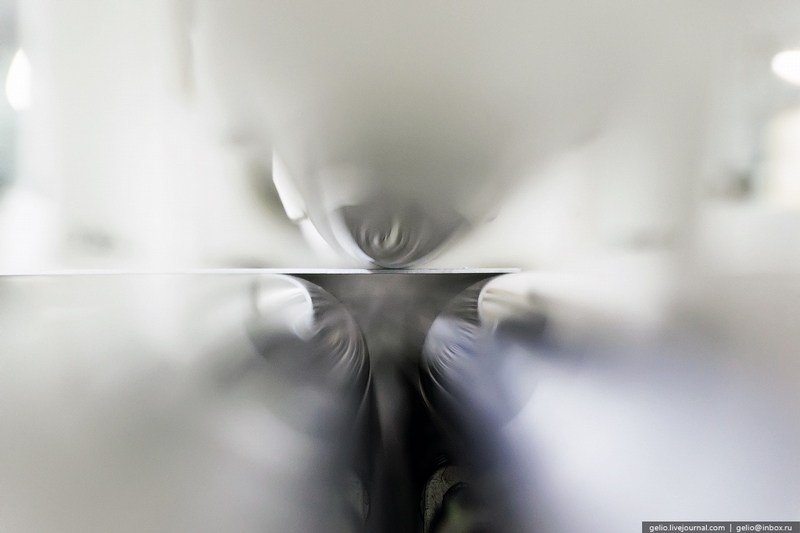
After the factory got some modern equipment the speed of production increased a lot. He says that for example, now one worker in one working shift can make something that required a four person team to work of one month. Its hard to believe. Here we've seen two shots from the workshop where the small parts are being pressed. He says that over 70% of the aircraft parts are being made here.
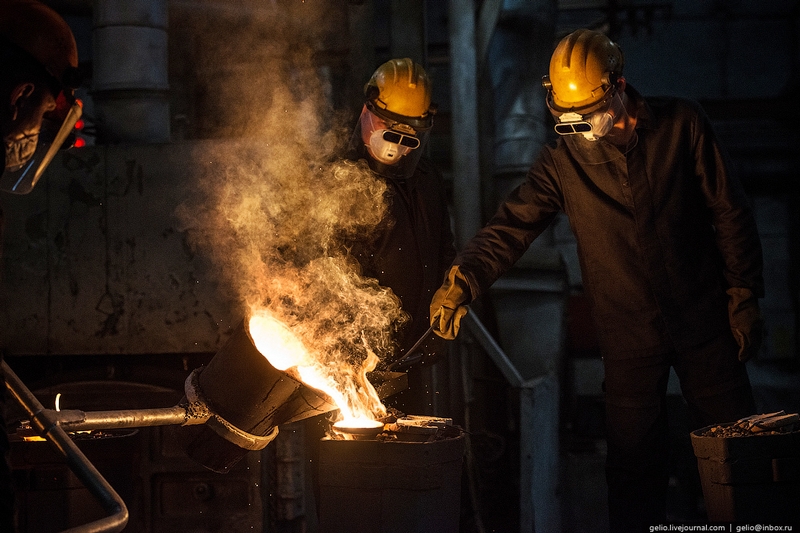
An example of the parts.
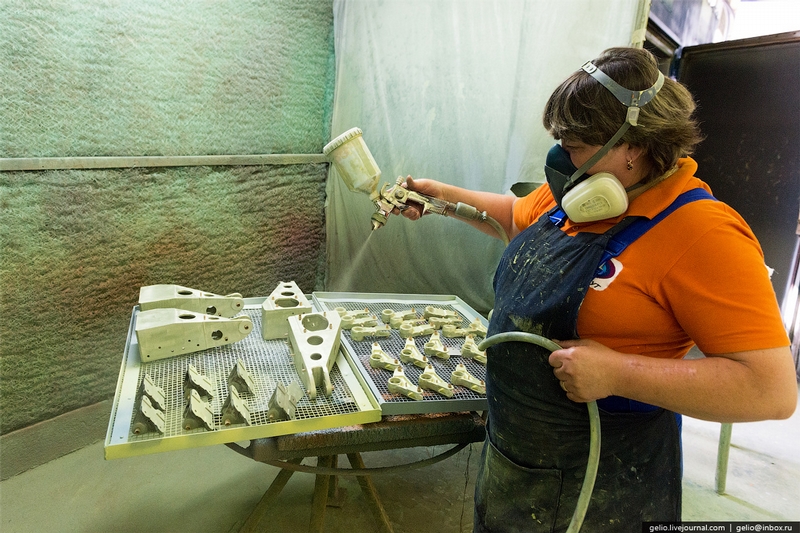
This is not regular paint, this is electroplating.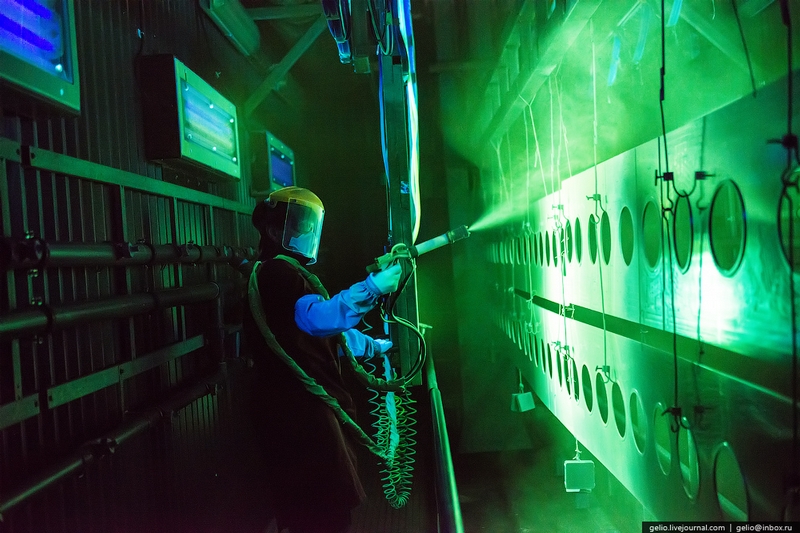
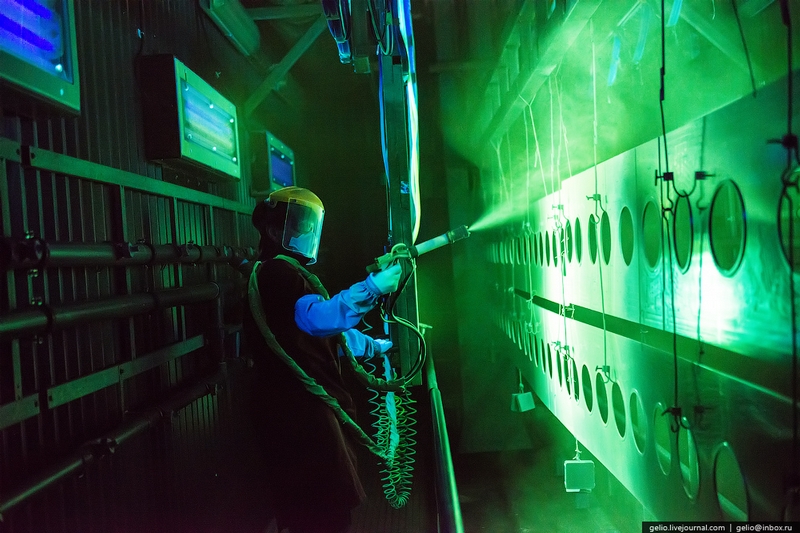
And here is a luminescent paint being sprayed on the parts, and then ultraviolet light is used to find the little, unseen with naked eye, defects of the manufacturing process.
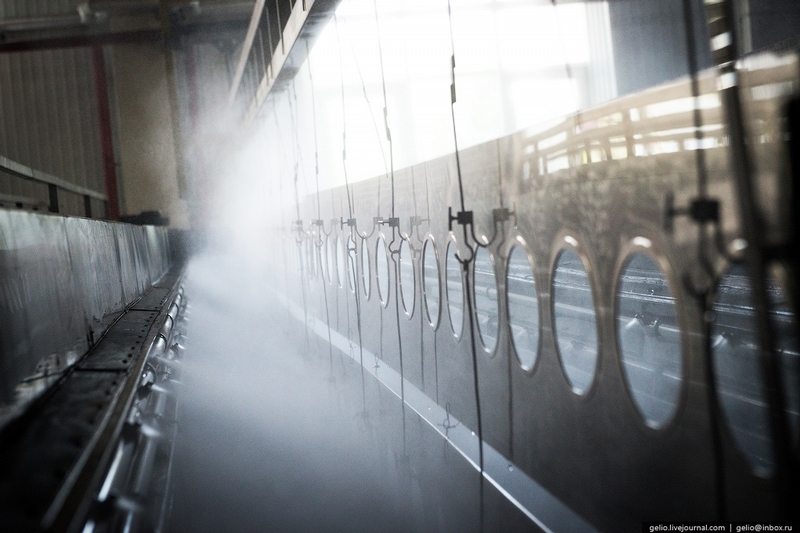
Like this, for example. This is an ultra-precise measuring machine, and with the help of some complex machinery it flies above the parts and tracks their geometry. If it finds even the slightest mistake the part doesn't pass quality control. I even doubt that they do this for the iPhone!
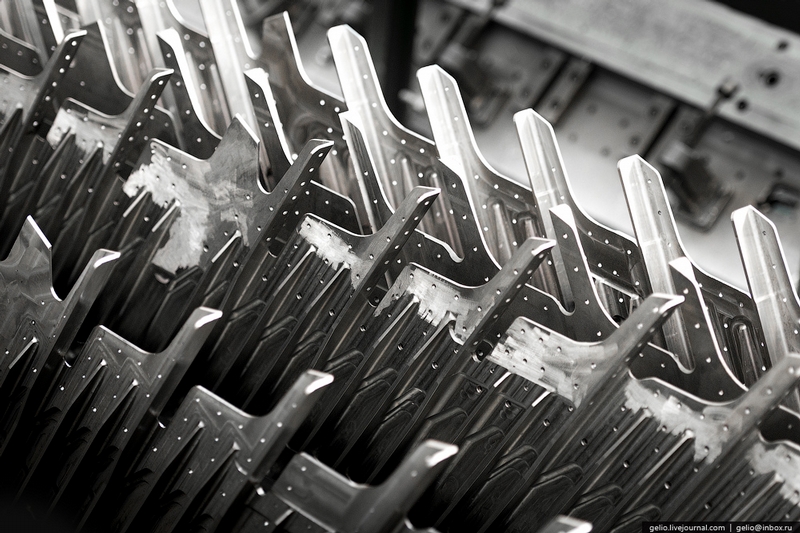
And then the smaller parts are being assembled into more complex parts.
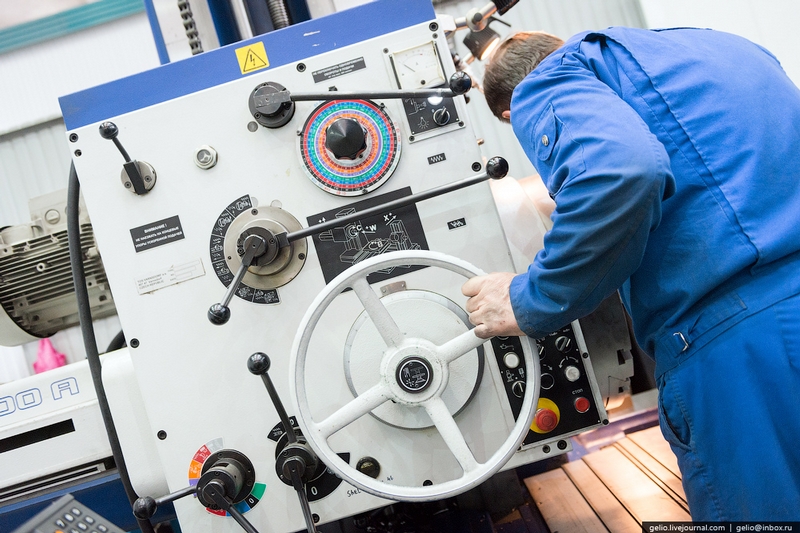
Making holes takes 80% of the time of this stage. Drilling!
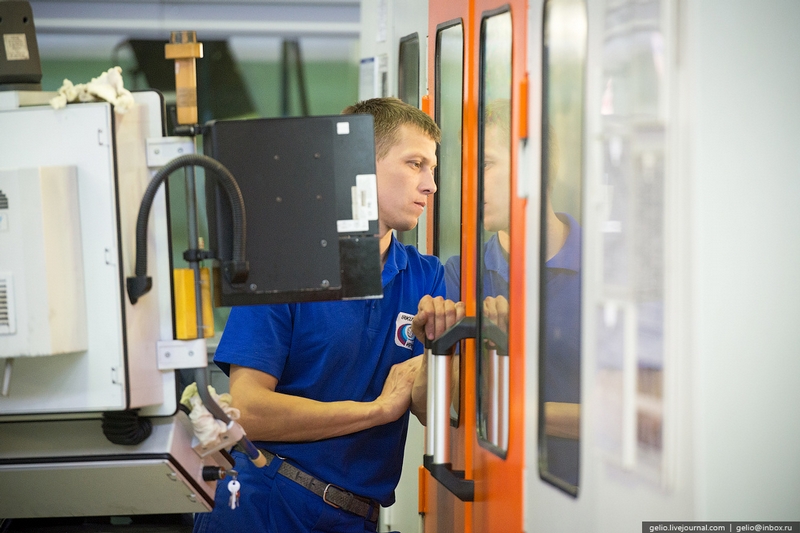
There is a separate testing unit.
Then the parts go back to the electroplating and coating workshop.
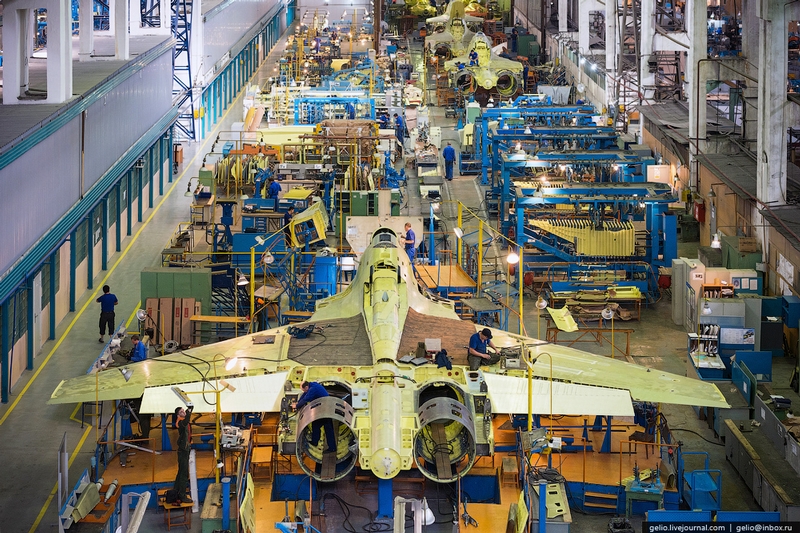
...and then those bigger complex parts are being assembled into the planes. This is an assembly line for SU-30 and SU-30SM.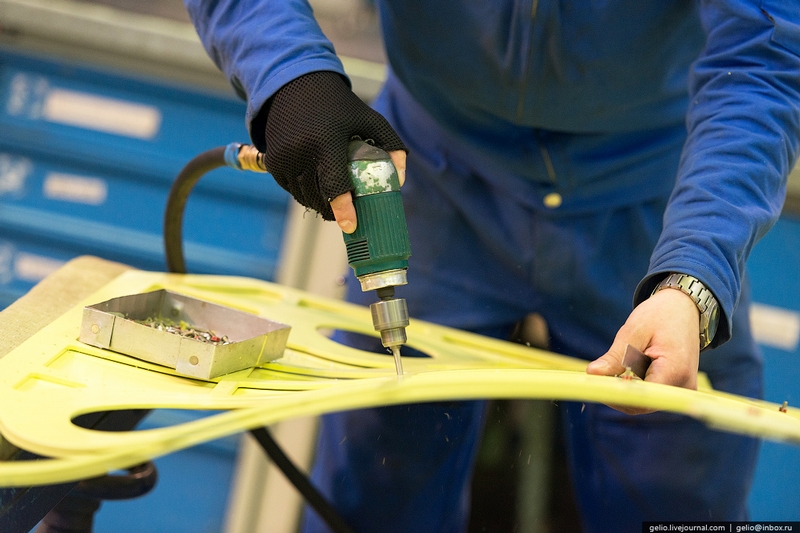
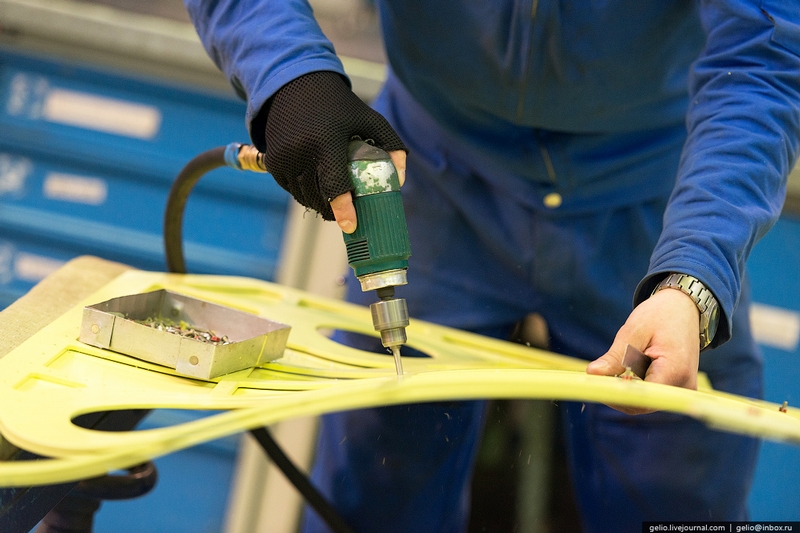
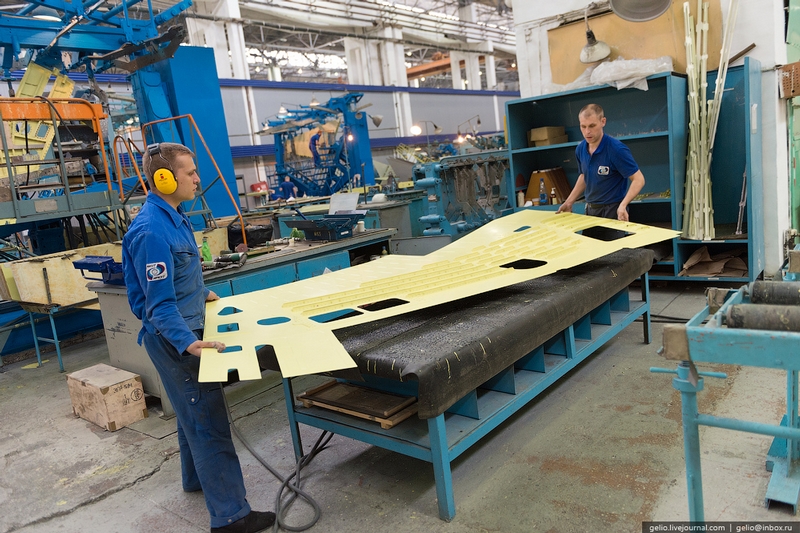
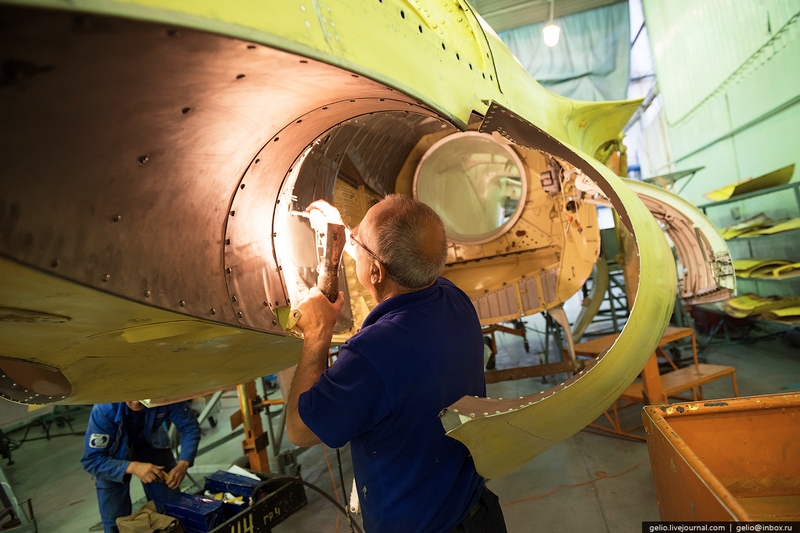
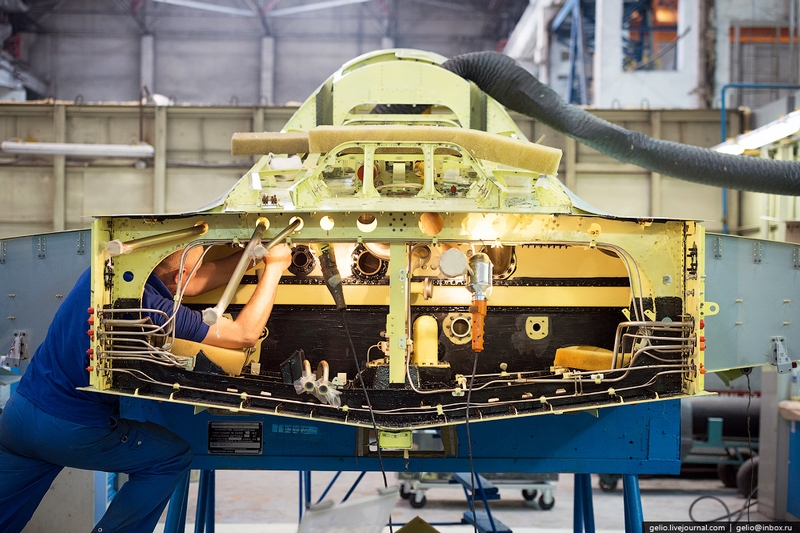
First flight of this YAK-130. On the conveyor
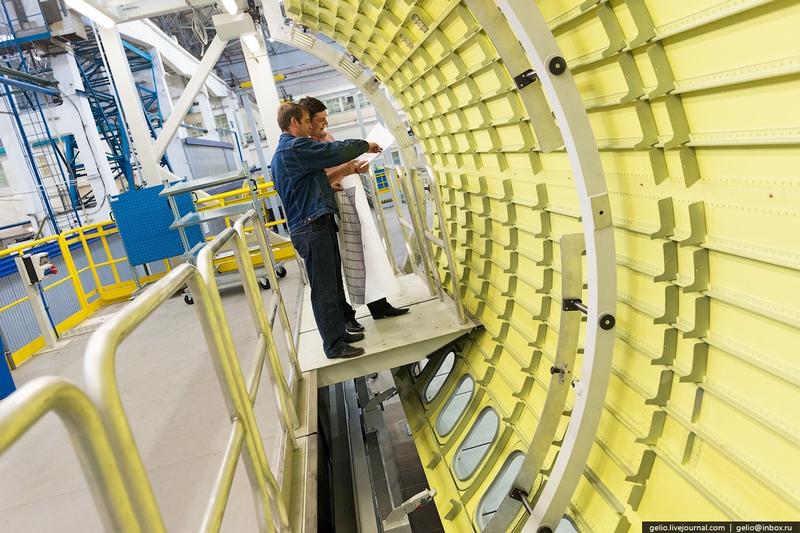
And this unit is a workshop for the final assembly, where the planes are being turned into working machines.
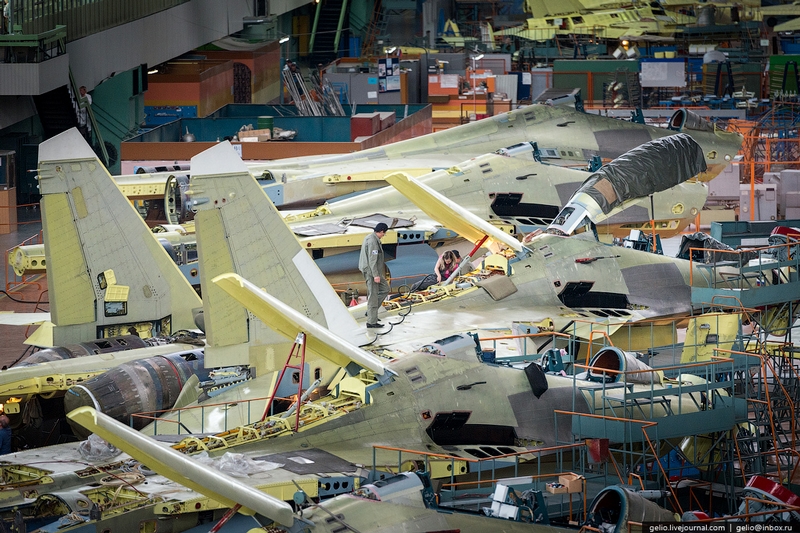
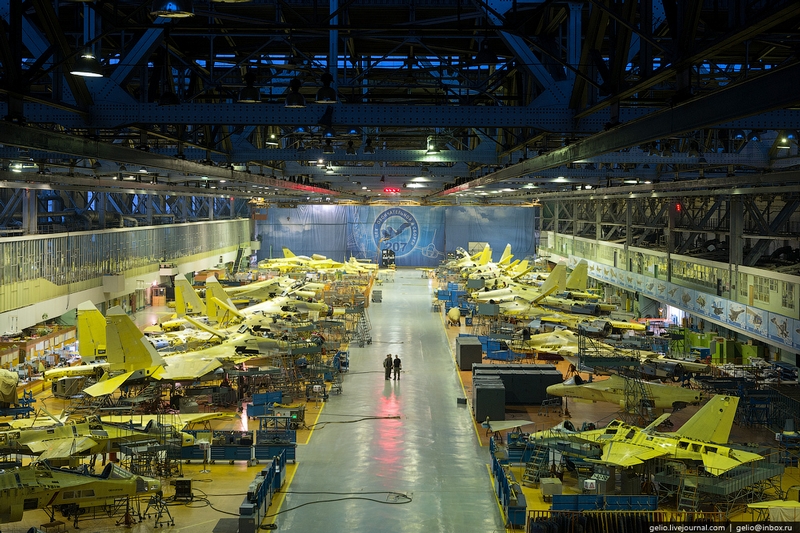
Most of the work is manual work. Sometimes people have to crouch to fit into the narrow spots and use the tools inside.
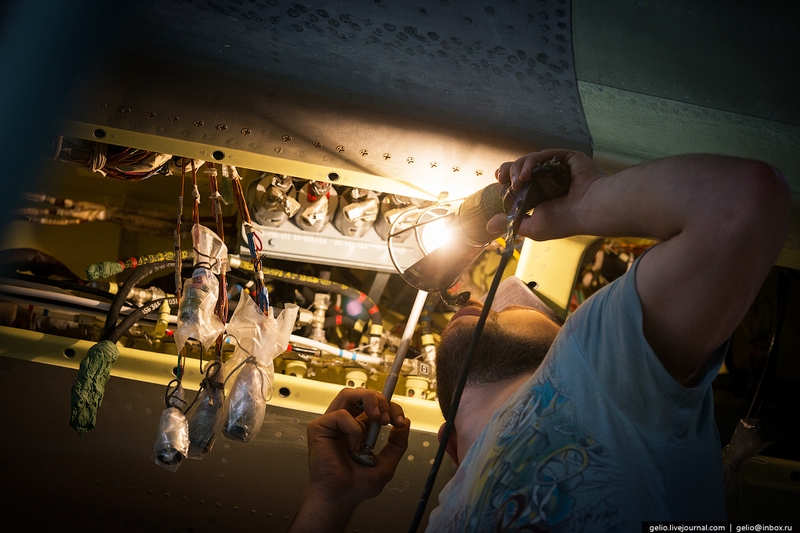
Total length of wiring in a YAK-130 is 30,000 meters. Wow. In a Su-30CM there is even more - 75,000 meters of wire is being used!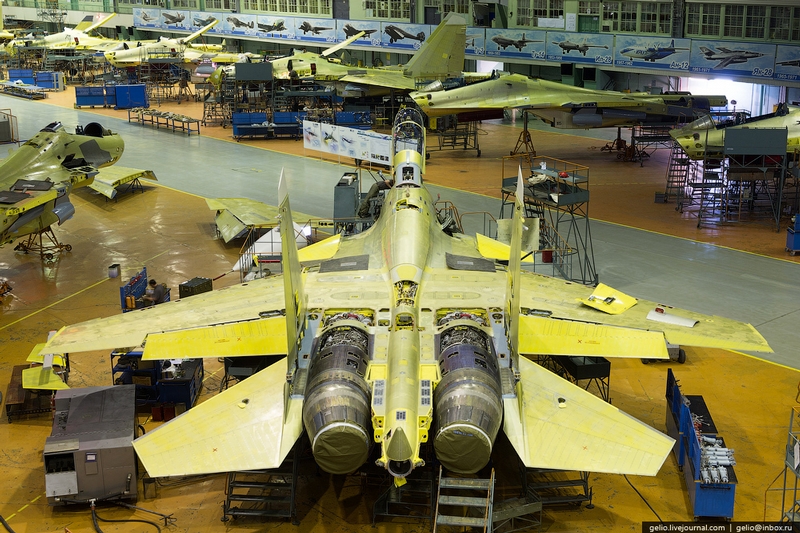
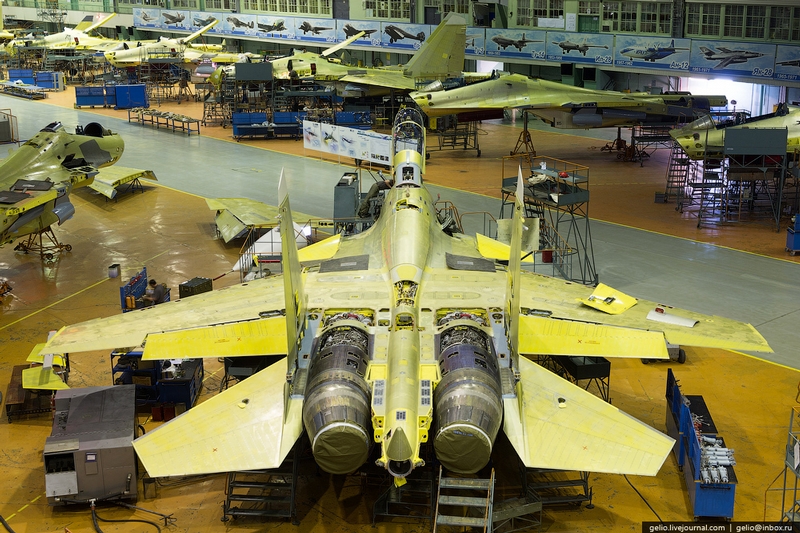
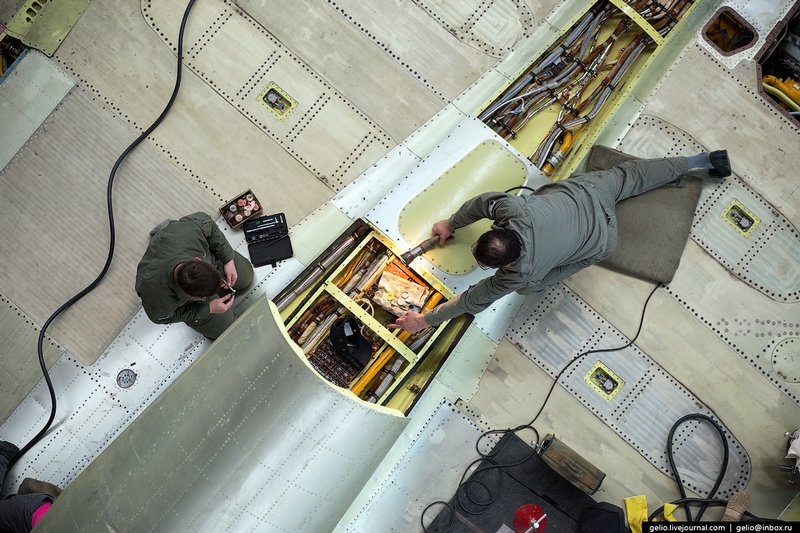
Why do they make YAK-130s - they're probably old planes by now? Because they are used to train pilots. Slava says that YAK-130s are the only training planes in the world that give the same feel as the newer models (SU-30, MiG-29, F-16, etc), so training on a smaller, cheaper plane almost prepares the pilots to fly the real thing.
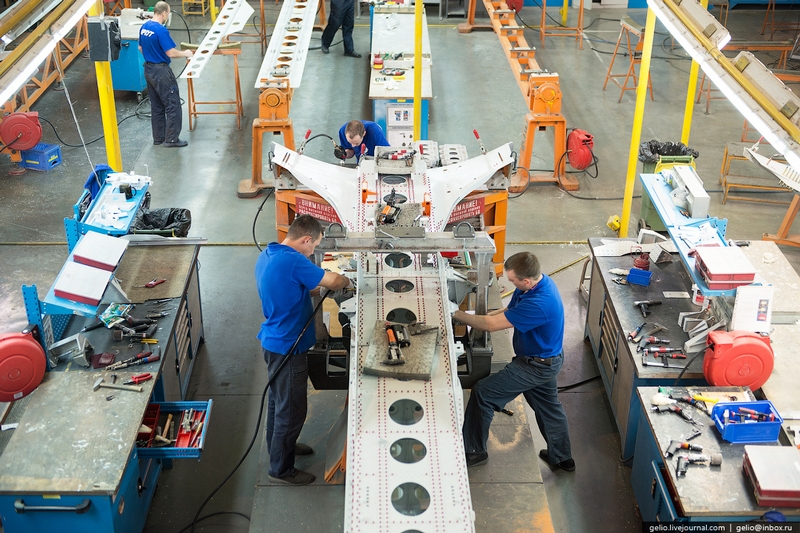
And this is a workshop of International cooperation, so they say. This is where they make AIRBUS parts, or more precisely, the parts for the A320 Airbus passenger jets.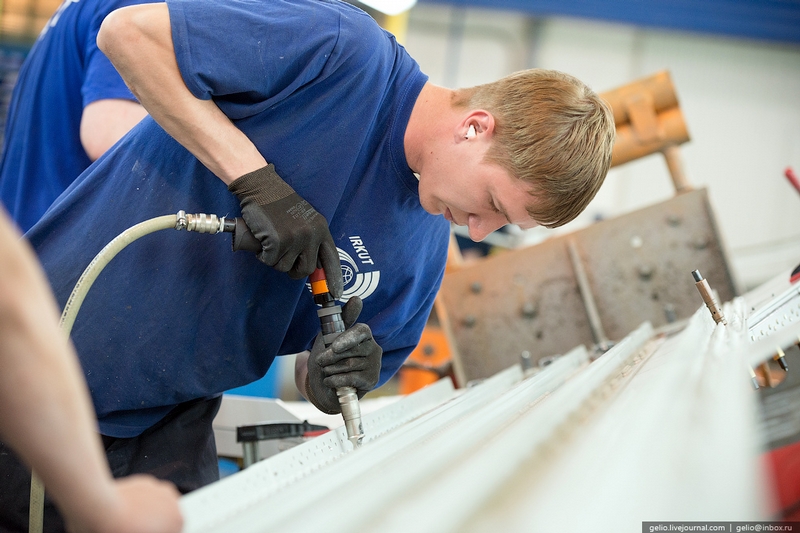
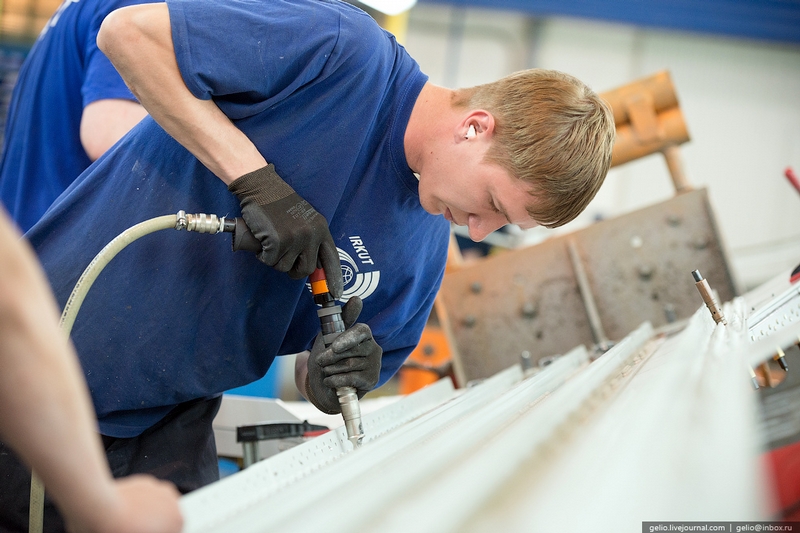
Almost every third AIRBUS A320 in the world gets a part that was manufactured here.
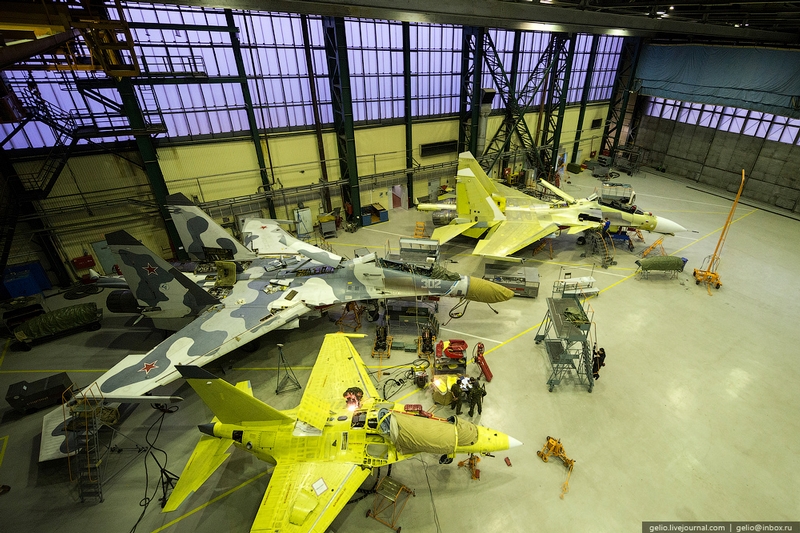
Only after this stage can the plane get its "passport" with a mark, "ready to use".
Comments