The Suspension System
Steering & Suspension
Steering & Suspension
The Steering system is a mechanism that enables the driver to guide and direct the vehicle in a chosen direction.
Suspension is the term given to the system of components, springs, shock absorbers and linkages that connects a vehicle to the road surface via the wheels and tyres.
Suspension systems serve a dual purpose — contributing to the car's road holding/handling and braking for good active safety and driving pleasure, and keeping vehicle occupants comfortable and reasonably well isolated from road noise, bumps, and vibrations.
These goals are generally at odds, so the tuning of suspensions involves finding the right compromise. It is important for the suspension to keep the wheels in contact with the road surface as much as possible, because all the forces acting on the vehicle do so through the contact patches of the tyres. The suspension also protects the vehicle itself and any cargo or luggage from damage and wear. The design of front and rear suspension of a car may be different but the following diagrams show a common type of system.
Front Suspension:

Front Suspension:

The steering wheel is connected to the rack and pinion system, which moves the wheels right and left via the inner and outer tie rods. These are connected using atrack rod end;
The track rod ends are adjusted to ensure the wheels are perfectly aligned (“Tracking”) and that tyre wear is minimised. The track rod end is a common wear item and simple to replace.
A CV joint (constant velocity joint) is part of a drive shaft (the shaft that attaches to a car’s transmission at one end and the wheel at the other). CV joints are designed to be able to bend in any direction while continuing to turn the drive wheels at a constant velocity. CV joints are mainly used in the drive shafts of front wheel drive cars.
Due to bumps and uneven surfaces in the road, a car's wheels tend to move up and down continuously while driving down the road; as a result, drive shafts cannot be made up of a solid shaft. The CV joint is used in front wheel drive cars because of its ability to maintain a constant drive force to the wheels despite the many different kinds of movements in the front end of the car. The CV joint is often used in rear wheel drive and four-wheel drive cars too. CV joints should be checked regularly and may need replacing as a car ages.
CV Boot
A CV joint is covered with a bulbous rubber boot that can deteriorate over time. When a CV boot cracks or tears open, the CV joint is exposed to the elements, which will quickly damage the joint. If the CV axles are inspected periodically, torn boots can be replaced as needed, potentially extending the life of the joints. If torn boots are left unattended, the joint or the entire axle may soon need to be replaced.
Rear Suspension:

Rear Suspension:

Springs & Shock Absorbers
Springs and Shock absorbers form part of your vehicle’s suspension system designed to reduce the effect of bumps and vibrations from road surfaces, providing you with a more comfortable ride. A good suspension system also helps to maintain vehicle stability and handling as well as helping to reduce your braking distance.
How it Works
When a spring is compressed and then released, the energy within the spring causes it to continue to flex up and down before it settles to its original shape. Going over a bump in your car compresses the springs, so the car would also continue to bounce up and down making the car difficult to control. The effect of the shock absorber is to dampen the spring’s natural reaction to bounce.
Shock absorbers are filled with hydraulic fluid or gas. When the shock absorber is compressed, this fluid is forced by a piston through a small hole in the shock absorber cylinder and into the other end of the unit. The design prevents this action happening quickly, so the spring is restricted from continuing to bounce, helping to keep all four tyres in good contact with the road surface.
Replacing Springs & Shocks
It can be difficult to recognise a problem with your suspension system because loss of performance occurs gradually over a period of time.
The spring works in an extremely harsh environment and over a mileage of 50,000 miles can move in excess of 500 million times. This leads to sagging or actual snapping. Poorly maintained roads and the prevalence of speed bumps has significantly increased the failure rates of springs in recent years.
To test your shock absorbers try this simple ‘bounce’ test. Press down on one corner of your car and let go. Count the number of bounces before the car comes to rest. If the car bounces even twice, your shock absorbers could be faulty and need to be checked.
Any suspension fault has a negative effect on your vehicles handling and safety characteristics and leads to premature tyre wear so it is always advisable to seek professional advice.
Our National Tyres and Autocare technicians can arrange this for you – call in at one of our branches (locate your nearest centre) or call 0808 256 9413 to arrange an appointment.
Suspension Arm
A suspension arm is designed to be attached to a vehicle's chassis; support the wheel hub and allow the suspension to move through its normal range of movement. The loadings on this component are immense and it has to work in extremes of heat, cold and extreme road conditions; a real 'hostile' environment!
Bushes
To connect the various metal components together and allow them to move in a smooth and controlled manner a bushing is used. In vehicle suspension systems, this can be synthetic rubber or polyurethane and separates the faces of two metal objects while allowing a certain amount of movement. This movement allows the suspension parts to move freely, for example, when traveling over a large bump, while minimizing transmission of noise and small vibrations through to the chassis of the vehicle. A rubber bushing may also be described as a flexible mounting or anti vibration mounting.
As you can see a vehicle’s steering and suspension system is a complex piece of engineering made up of many components that work together to maintain a safe, controlled and comfortable ride by ensuring maximum Steering, Stability & Stopping for your vehicle.
Due to the harsh environment in which this system operates it is essential that it is checked and maintained on a regular basis.
Should you need to replace any of your vehicle’s steering or suspension components, whether it be CV Joints, CV Boot Kits, Drive Shafts, Hub Bearing Kits, Road springs, Shock Absorbers, Steering Racks, Bushes, Tie Rod Ends or Ball Joints just contact your nearest National Tyres and Autocare branch on the number at the top of this page. Don’t forget to take your discount voucher, available to download from our Special Offers page.
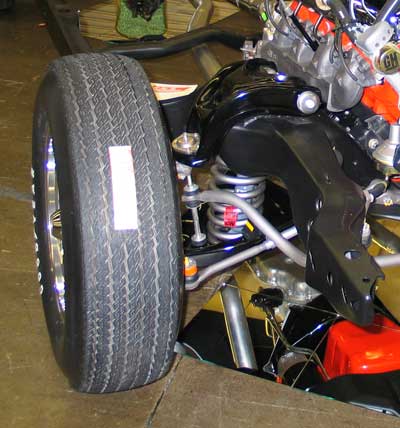
When to replace struts and shocks on your car.
Your suspension soaks up the bumps in the road, keeping you comfortable and safe by allowing your brakes and tires to work as designed. Let's look at the major components and then talk a little about what can go wrong.
Spring:
Springs allow your car to absorb the energy of a bump or pothole, without jarring the occupants of the car. Most cars have 4 springs made from spring steel (huh imagine that!) and wound in a spiral shape. Some cars (Corvette) have transverse (across) springs and are made from fiberglass or other composite materials. Made to last the lifetime of the vehicle, properly sized springs seldom need to be replaced.
Shock:
Shocks work to dampen the springs natural tendancy to oscillate. A good way to test your shocks is to push on a corner of your car and observe how many times the car bounces. More than twice and your shocks are worn. The shock is designed with fluid and internal passages to control the movement of the wheel and dampen the spring, over time the fluid can leak, degrade or the valving can become damaged.
Strut:
Just a fancy unit that combines the spring and shock in to one unit. Usually a little more labor to remove the spring when replacing the shock (strut cartridge).
MacPherson Strut:
Just a fancier version of the Strut which also serves as the upper pivot point for the suspension.
Sway or Roll Bar:
When cornering the forces want to roll your car's body to the outside of the turn. You feel this same force sitting inside the car. The Sway Bar counteracts this force and helps to keep the inside wheel in contact with the ground. Stiffer Sway Bar rates give a firmer ride, but better handling.
Ball Joints:
Your suspension is designed to move up and down with the road. This is accomplished with control arms which are connected to the spindle by ball joints. They are what they sound like, a ball and socket joint which allows movement in two dimensions. Most modern ball joints are lubricated with grease, and are sealed. Older ball joint and some newer truck ball joint do have a grease fitting to allow adding grease.
Spindle:
The spindle serves as the center point for your wheel, and rotor to rotate around. The spindle also connects to the lower control arm and upper control arm or MacPherson Strut. Through the travel of your suspension the spindle should remain as parallel to the road as possible. Suspension geometry is designed to keep as much of the tire in contact with the road as possible.
Common Problems:
- Shocks and struts can wear out and affect handling. If you car bounces excessively over bumps and leans hard in corners, your shocks could be warn. Look behind the wheel for the shock or strut and look for leaking oil. This is a sure sign of a worn shock or strut. Also check your owners manual, some will give a mileage estimate for shock or strut life. As a general rule somewhere in the 60,000 - 75,000 mile range depending on your driving style and road conditions.
- Ball joints. Ball joints wear and can cause your car to wander while driving down the road. This is dangerous as they can separate and cause you to lose control.
- Sway bar bushings can wear out over time and will allow the sway bar to clunk when turning corners or at low speeds. A fairly inexpensive part to replace, but gaining access can be tricky depending on the vehicle.
Preventive maintenance:
- Check your shocks or struts for leakage frequently. Also pay attention to how your car handles. If you notice the ride deteriorating take your car in to have the struts checked.
- Ball joints should be checked when your car is inspected, if not, have your mechanic check them at least twice a year.
- At each oil change make sure you or your mechanic lubricates the ball joints and any other suspension components. Some components can not be lubricated as they are sealed from the factory.
Inspect Car Suspension
Copyright AA1Car.com
Adapted from an article written by Larry Carley for Brake & Front End magazine
The suspension or chassis is not something to neglect because it supports your vehicle and affects steering, handling, braking, tire wear and ride. How many times have you seen a vehicle broken down on the side of the road with a collapsed suspension because a ball joint failed, or the front wheels are splayed in opposite directions because a tie rod end separated? Fortunately, these kinds of catastrophic failures don't happen that often, but when they do they can have tragic consequences.
So here are some of the things you should inspect or check on your vehicle's steering and suspension when doing brake work, changing tires, exhaust repairs or an oil change.
- Check all four tires for uneven wear, cupping or tread damage.
- Check the steering linkage for play.
- Check for leaks in power steering hoses and the steering gear.
- Check the condition of the shocks and struts.
- Check all four wheel bearings for play or roughness.
- Check the ball joints for play or wear.
- Check the suspension bushings front and rear.
- Check all the springs for damage.
- Check for leaky or damaged CV joint boots.
- Check for leaks at the differential, transmission or transaxle.
START WITH THE TIRES
Unusual tire wear is a dead giveaway that a vehicle has either an alignment problem or worn/damaged steering or suspension parts. What to look for:
- Toe wear can produce a feathered wear pattern across both front tires and sometimes shoulder wear on the inner or outer edge of both tires. Toe wear is usually caused by worn tie rod ends, but may also result from worn or loose inner tie rod sockets on rack & pinion steering gears. Other causes include bent steering arms or misalignment in the rear wheels.
If toe wear is accompanied by steering looseness or steering wander, there is a very good chance the tie rod ends are worn. Proceed to the steering checks. If toe wear is accompanied by a steering pull or off-center steering, rear wheel toe alignment or axle alignment may be out of specification.
- Camber wear causes uneven wear on one side of a tire may show up when control arm bushings have collapsed, ball joints are loose, a spindle or strut is bent, or a strut tower is out of its normal position (due to factory misassembly, collision damage, body sag or severe corrosion). Another overlooked cause of camber wear can be a front-wheel drive engine cradle that has shifted out of position to one side. A weak or broken spring can also allow camber changes in the suspension that produce camber wear on a tire.
- Cupped wear may be the result of badly worn shocks or struts, or wheel and tire imbalance.
STEERING CHECKS
The steering can be inspected in one of several ways. With the full weight of the vehicle on the wheels, have a helper rock the steering wheel while you look for play or looseness in the steering linkage and steering column. On some vehicles, this can be done by reaching up and rocking the steering column coupling from underneath while the vehicle is sitting on a drive-on ramp style lift. The dry park method of checking for looseness is generally the best procedure to use because the weight of the vehicle on the wheels creates resistance that makes it easier to see play.
The dry park method is also a good way to find loose upper strut bearing assemblies. While rocking the steering back and forth, watch for strut movement in the strut tower opening. Any wobble would tell you the strut bearing plate is worn and needs to be replaced.
As a rule, tie rod ends should show no visible vertical or horizontal play during the dry park check.
The inner tie rod sockets on rack & pinion steering gears are enclosed in bellows, making them difficult to inspect. If the bellows are rubber, you can check for looseness by squeezing the bellows and pinching each socket while pushing outward on the wheel or while a helper rocks the steering wheel. If you feel movement, the sockets are loose and need to be replaced. You can't do this check with hard plastic bellows, so lock the steering wheel with a holder and watch for any in or out movement in the tie rod while pulling and pushing on the wheels.
Also pay attention to the rack mounts. Loose, deteriorated or broken mounts may allow the rack housing to move as the wheels are turned. This can cause steering wander and noise.
With reciprocating ball steering systems, pay close attention to the amount of play in the idler arm. Looseness here can cause steering wander and toe wear. Pitman arms should show no vertical looseness. Center links should be like tie rod ends and show no vertical or horizontal play.
If the vehicle is not your own, take it for a test drive. Pay attention to things like steering effort, return, stability, feel and noise.
POWER STEERING CHECKS
Steering effort on both manual and power systems should be checked with the weight of the vehicle on the wheels. Unusually high effort combined with poor steering return may indicate a weak pump or a worn spool valve in the steering rack. Other causes of increased steering effort can include binding in the steering rack, improper rack yoke adjustment, and binding in tie rod ends, ball joints or upper strut bearing assemblies. Power steering can also be checked with the wheels off the ground. If the steering wants to turn to one side when the engine is running, it indicates a problem in the control valve.
Don't forget to check the fluid level in the power steering pump reservoir, too. A low level may indicate leakage. A visual check of the pump, hoses and steering gear should reveal the source.
If the fluid is badly discolored (dark brown with a burnt smell), the fluid has been overheated and is oxidized. This can doom the pump and steering gear to premature failure (if they have not suffered damage already). Replacing the fluid may buy these parts some time.
Some hissing noise is normal with most power steering systems, but excessive noise may indicate a bad check valve. Belt squeal would tell you the belt needs to be tightened or replaced. Pump noise usually indicates wear.
WHEEL BEARINGSCheck the wheel bearings for play before proceeding on to the ball joints, because play here can mimic loose suspension parts and contribute to steering wander and instability.
Start by raising the wheels off the ground and spinning each wheel by hand to check for roughness or noise in the bearings. Do not confuse normal brake drag for bearing noise. If the bearings are rumbling or clicking, removal for cleaning and further inspection will be necessary unless the bearings are the sealed variety, in which case replacement would be required if they are making noise, loose or rough.
To check wheel bearing play, grasp the wheel at the top and bottom, then try to rock it back and forth by pushing in with one hand while simultaneously pulling outward with the other hand. Alternate back and forth to see if the wheel rocks or moves. If you feel movement, the bearings are loose. Refer to specifications for the maximum allowable play.
Serviceable wheel bearings on older vehicles should be removed, cleaned, inspected, repacked with fresh grease (new grease seals, too!) every 30,000 miles for preventive maintenance. They should also be removed, cleaned and inspected if the vehicle has been in hub-deep water, or if the bearings feel loose or out of adjustment.
If a sealed bearing and hub assembly is loose, feels rough when spun by hand or is making noise, it needs to be replaced.
NEXT, THE BALL JOINTSIf the ball joints have built-in wear indicators, joint play should be checked with the weight of the vehicle on the wheels. Ball joints without built-in wear indicators are generally checked by raising the suspension to take the weight off of the joints. Procedures vary.
On rear-wheel drive applications with SLA suspensions where the spring is on the lower control arm, modified strut suspensions which also have the spring on the lower control arm, and front-wheel drive wishbone strut suspensions where the spring is on the strut, but the strut is connected to the lower control arm, the lower ball joints carry the weight and must be unloaded to measure play. This is done by raising the vehicle and supporting the lower control arms to take the weight off the lower ball joints, then pulling on or prying against the wheel (not the ball joint!) to measure vertical and horizontal play in both the lower and upper ball joints. Also, make sure the ball joint is securely attached to the control arm by looking for any signs of movement between the housing and arm.
If an SLA suspension has the coil spring over the top arm, the upper joints are loaded. To check these joints, the vehicle has to be raised and the upper control arms blocked or supported to unload the upper joints.
With MacPherson struts, the strut supports the load, so the lower ball joints are unloaded. To measure play, simply raise the vehicle and allow the suspension to hang free. Then push on or pry against the wheel to measure vertical and horizontal play in the lower ball joints.
To check rear ball joints on a FWD car with an independent rear suspension, raising the wheels and supporting the suspension arms will unload the joints.
Note: All ball joints should be checked prior to lubricating the chassis (if joints are greaseable) because grease may temporarily take up slack in the joint.
The amount of horizontal (radial) and vertical (axial) play that is allowed in a ball joint will vary depending on the joint type, location and vehicle application. Always refer to the vehicle manufacturer specifications, and use a dial indicator to measure the amount of play unless the joint is obviously shot.
CONTROL ARMS, BUSHINGS & SWAY BARSFront control arms, as well as rear trailing arms and lateral links, should all be visually inspected for damage or cracks. Also, make sure the ball joint is securely attached to the arm.
Check the bushings for excessive movement, deterioration, cracking or crush. This can be done by gently prying against the control arm to see if the bushings allow much movement. A little "give" with rubber and elastomer bushings is normal, but if you see more than about 1/8 inch, it may mean the bushing has collapsed. Metal bushings should have little or no play. Bouncing the suspension can help you identify noisy bushings.
On sway bars, check the sway bar bushings and mountings. The mountings should be securely attached to the chassis, and the bushings should be in good condition (no cracks, splits, crushing, etc.). Check the end links of the sway bar and their bushings, too, for looseness. If the ends of the sway bar are attached directly to the control arms, check to see that the mounting is secure.
SHOCKS & STRUTSA "bounce test" will usually reveal shocks that are badly worn, but a test drive will give you a more accurate picture of their condition. If the vehicle sways excessively, rocks, feels bouncy or otherwise lacks proper ride control, you should recommend new dampers.
When visually inspecting the shocks and strut assemblies, look for:
- Physical damage (broken mountings, bent rods, etc.);
- Fluid leakage (which indicates seal failure);
- Loose, collapsed or cracked rubber mounting bushings; and
- Physical contact with other suspension components, exhaust pipes or brake lines.
Any of the above conditions would call for repairs or replacement.
DON'T FORGET TO CHECK RIDE HEIGHTMeasuring ride height will tell you if the springs are sagging. Notice we said "measure." That doesn't mean take a quick glance and let it go at that. It is hard to see small but significant differences in ride height side-to-side, and virtually impossible to tell if a vehicle is within the factory-specified ride height dimensions without using some type of measuring device.
If ride height is below specification, the springs are sagging and replacement is recommended. Also, keep in mind how you use your vehicle. For some applications, upgrading to variable-rate springs can provide extra load carrying capacity as well as improved handling when pulling a trailer.
Adapted from an article written by Larry Carley for Brake & Front End magazine
Comments